The family-run brickwork business Vandersanden has created CO2-negative facing bricks that necessitate fewer raw materials and absorb carbon dioxide rather than produce it – a world first.
The bricks are created from steel industry residues, mixed with fine sand and hardened with CO2: a process known as carbonation that results in a hard limestone-like stone. Carbonation not only absorbs CO2 but also does not create additional carbon dioxide since it doesn't necessitate a kiln. The production of one ton of material absorbs at least 60 kg of CO2.
"It took years of hard work to develop a circular, CO2-negative facing brick," Rudi Peeters, Vandersanden's CEO told L'Echo. "This brick is a milestone for our sector. With it, we are contributing, as a manufacturer, to greater circularity and a reduction in the CO2 footprint throughout the construction sector."
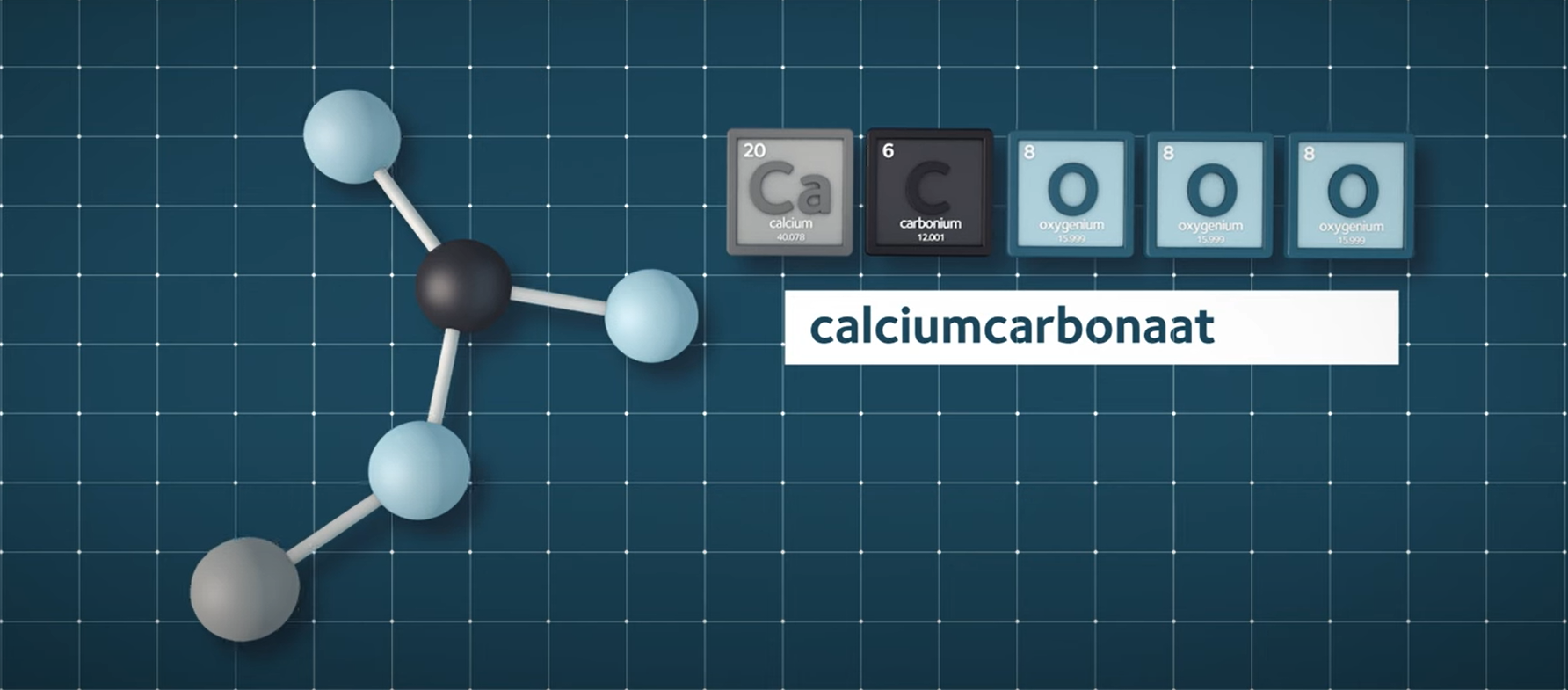
An illustration of the calcium carbonate molecule that results from carbonation. Credit: Vandersanden
The process was perfected by the company Orbix and applied to front-facing bricks (the ones on the exterior façades of buildings) by Vandersanden.
In line with the company's "Together to Zero" campaign, the first factory for these CO2-negative bricks—branded Pirrouet by the company— is currently being built in Lanklaar, Belgium and will run on power generated by solar panels and wind turbines. Starting next year, the factory will be able to produce an annual 20 million COz-negative bricks a year.
The aim is to build these factories close to heavy industries in order to offset their CO2 production.
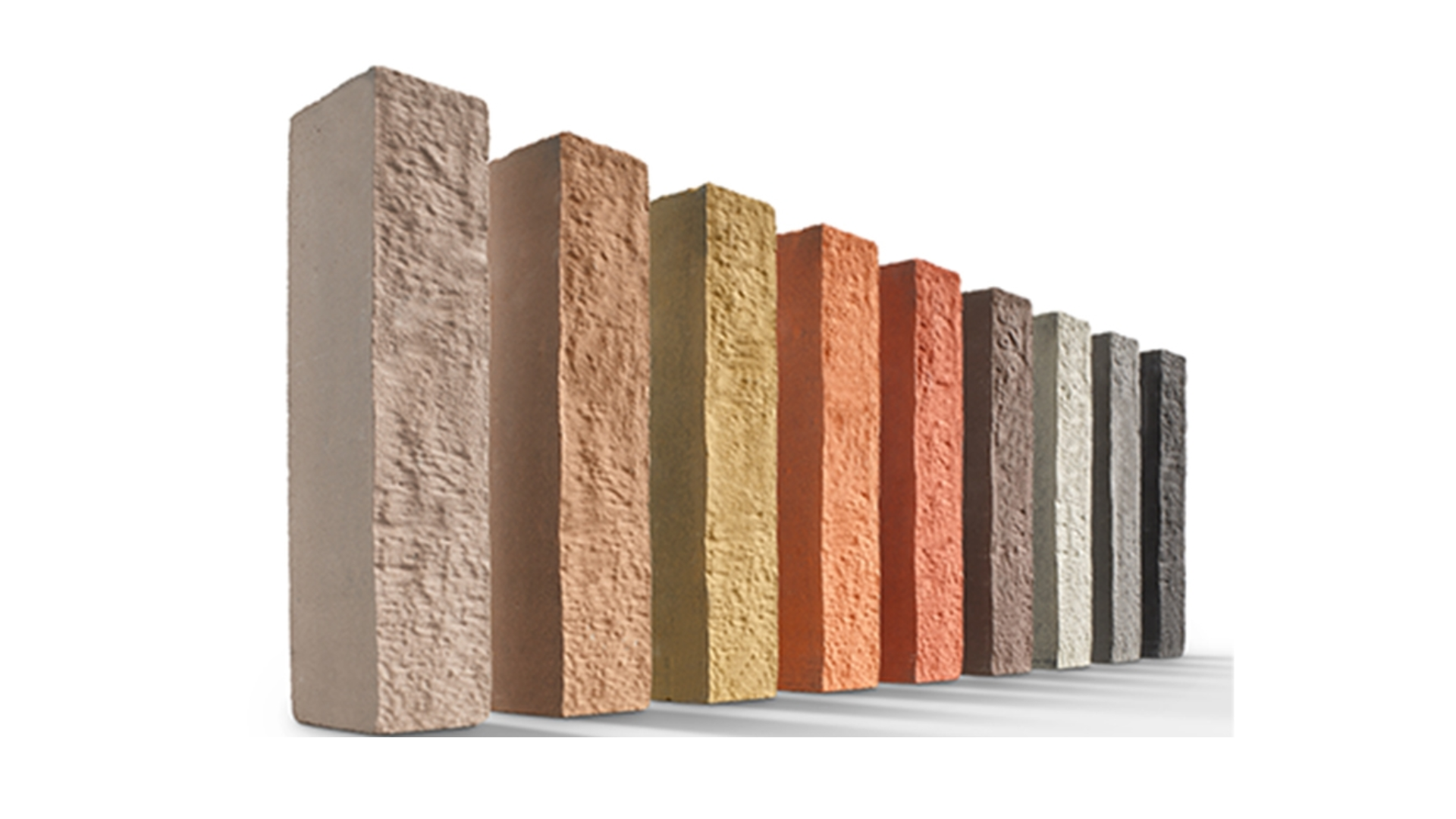
The nine shades of colour that Pirrouet bricks will be available in. Credit: Vandersanden
"From industries with high emissions, such as the steel industry, which will transport it to the Lanklaar plant. Eventually, we intend to capture and transform our own emissions too, although there are relatively few of them," Peeters told L'Echo. Aperam will be the first company to partner with Vandersanden, with steelmaker ArcelorMittal to join soon after.
The family's ambitious goal is to eventually reach the production of up to 100 million CO2-negative bricks a year.