They say Belgians are born with a brick in their stomach, which requires plenty of mortar to create the buildings we know and love. But the country's heavy use of concrete is a significant environmental concern as cement, the key binding agent, emits huge amounts of carbon dioxide (CO2) emissions.
It's a problem that industry leaders are aware of and seeking to solve. Cement production currently contributes to 3% of global energy consumption and is responsible for approximately 4.5% of global greenhouse gas emissions.
Addressing the environmental impact of cement production is crucial to achieving the ambitious goal of limiting global warming to 1.5℃, a target discussed once again at the UN Climate Change Conference which is taking place in the United Arab Emirates until Dec. 12.
According to the Environment Ministry, the cement sector accounts for 3% of Belgium's total CO2 emissions but a remarkable 31% of Wallonia's.
Several Belgian companies are working towards reducing the environmental impact of cement production, but they face the challenge that a substantial portion of emissions arises from the calcination process – a stubborn hurdle to decarbonisation.
Changing the traditional recipe
Calcination involves heating limestone and clay to create clinker, key to cement production. The process accounts for around 60% of all CO2 emissions from cement production. Unlike other steps that can be decarbonised with renewable energy sources, altering the chemistry of cement production poses a unique challenge. Meanwhile the increasing demand for cement amplifies the urgency to find sustainable solutions.
Interest in low-carbon cement has surged as an alternative to ordinary Portland cement (OPC), which is around 90% clinker and emits 0.6 tons of CO2 per ton of cement. By contrast, low-carbon cement has the potential to slash process emissions by anywhere from 10 to 100%.
One effective strategy is to reduce the amount of clinker in cement by incorporating supplementary cementitious materials (SCMs) or fillers. SCMs, such as fly ash and granulated blast furnace slag, react chemically with clinker, offering a way to reduce emissions.
While the challenge lies in decreasing the clinker-to-cement ratio, identifying new sources of quality SCMs presents a significant opportunity for companies looking towards a low-carbon cement solution.
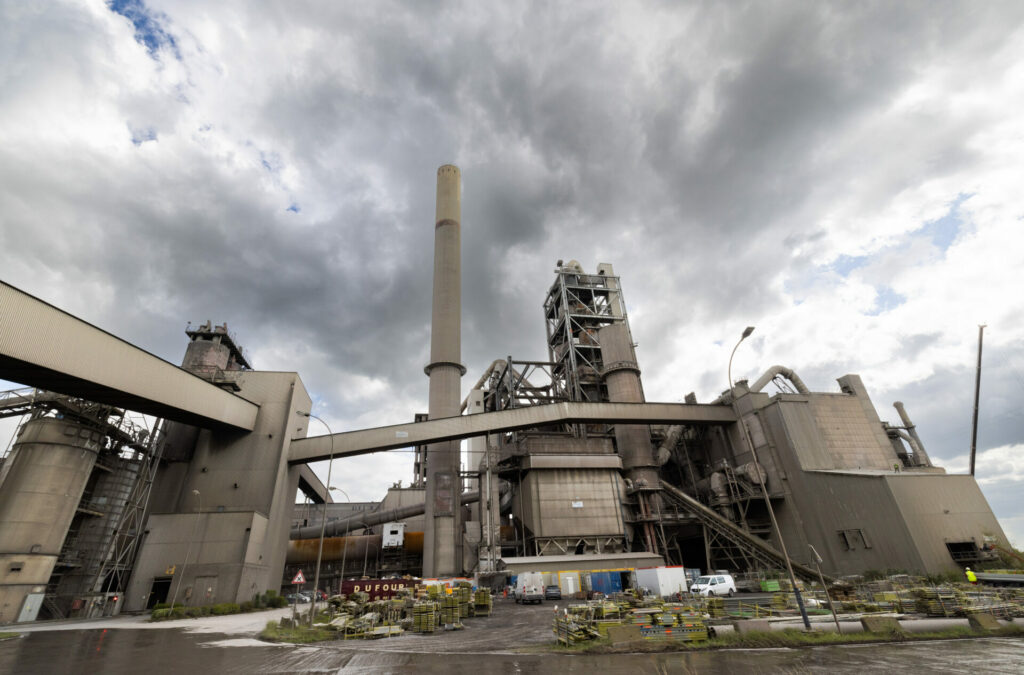
The cement industry is a huge source of CO2 emissions in Wallonia, but it's an industry stuck in its ways. Credit: Belga
Another approach is to change how clinker is made. This might be by reducing limestone content or exploring alternative calcination processes, such as hydrothermal or electrochemical methods. The challenge is to make this less complex and cost-effective.
The most ambitious approach is to reformulate cement recipes entirely. Innovations like alkali-activated binders, geopolymers, and magnesium-based cement have the potential to eliminate or significantly reduce clinker in the production process.
Related News
- After a flying start, COP28 stumbles on future of fossil fuels
- Europe's green future depends on saving the energy debate from a 'dogmatic sect'
However, while the low-carbon cement revolution is slowly gaining momentum, it faces deep-rooted scepticism from within the industry as well as limited data on energy use and concerns about the availability of raw materials.
As the Belgian cement industry embarks on this transformative journey, questions linger about the feasibility and impact of developing sustainable solutions. The push towards low-carbon cement production remains a critical component in the broader ecological roadmap, with ongoing debates surrounding the industry's commitment and the effectiveness of its proposed solutions.
The future of construction in Belgium may well hinge on the industry's ability to navigate this challenging path towards sustainability.
On a global scale, the shift to low-carbon concrete is not just an environmental imperative, it is an investment in a sustainable and resilient future for generations to come.