The slick opening promotional video on the Audi Brussels website gives little hint of impending doom.
Far from it. Against the backdrop of a suitably propulsive soundtrack, the footage begins with a dramatic aerial shot of the sprawling urban plant in Forest (Vorst), located to the west of the city centre next to the ring road. The camera pans down to the carbon-neutral factory’s expansive roof-top, covered in solar panels. It’s a message. In case the viewer doesn’t immediately catch on, the word “sustainability” pops up, followed by “we set the course…for a sustainable future.”
It’s a line that hasn’t aged well.
The camera then takes us inside the state-of-the-art, 1.5 km long, spotless assembly hall, capable of producing nearly 200 Audi Q8 e-tron models a day. We see lines of gleaming, dancing yellow robots, busy building out the skeletons of each car – lifting, drilling, fixing and welding hundreds of the parts which go into the construction of each electric vehicle (EV).
There are humans in the picture, too, doing highly skilled things. Men and women of varying ages and from different backgrounds. This diversity is highlighted in the video with a series of beaming portraits of smiling employees, overlaid with the word “together”. A happy worker peers through a partially built car and forms a heart shape with his hands.
Just over two minutes long, the film ends with the line: “Audi Brussels. Where we create masterpieces with passion” – a nod perhaps towards Belgium’s artistic heritage.
It seems a tad surprising no-one has thought of taking it down, in view of recent developments which have left nearly 3,000 workers facing a precarious future.
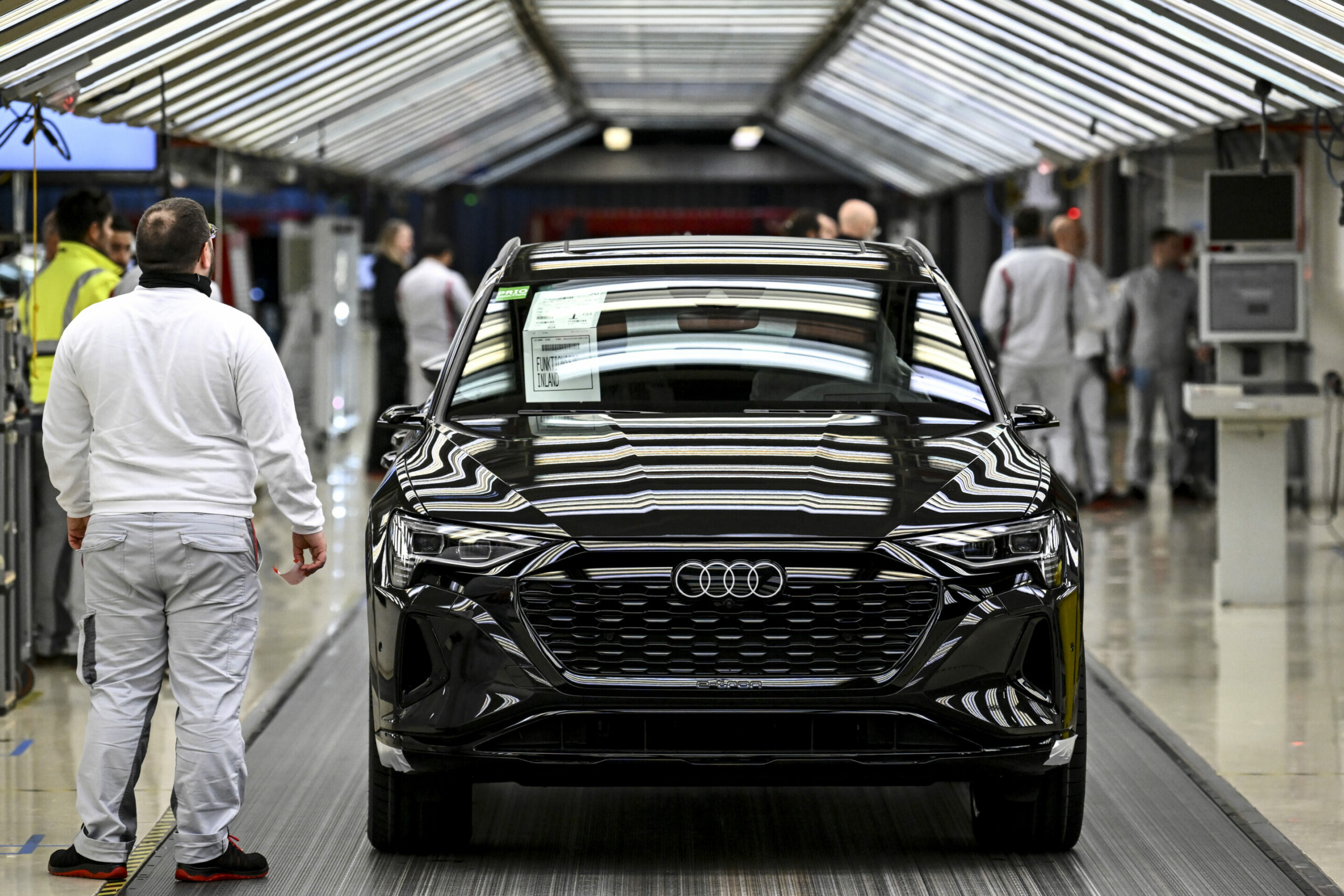
At a press invitiation for the start of production of the Q8 e-tron and Q8 Sportback e-tron at the Brussels plant in Forest, Wednesday 14 December 2022. Credit: Belga / Dirk Waem
The bombshell news of the plant’s “restructuring” – in the eyes of many a euphemism for its likely permanent closure – came in the second week of July, just before it shut for the summer break. By late October, Audi confirmed the worst: it would end production at the Brussels plant in February 2025. The management has also promised that there will be no redundancies in 2024 and is continuing its search for a buyer.
Audi blamed its decision on a sharp drop in orders for its flagship Q8 e-tron models, amid increasing competition in the electric luxury class market where the four-ring brand is up against Tesla, Volvo, Mercedes, BMW, Jaguar and Porsche, as well as subsidised Chinese makes. The German carmaker also pointed to “long-standing structural challenges” which have dogged the site in Forest.
Production of the Q8 e-tron is expected to move to Audi’s newest plant at San José Chiapa in Mexico, where labour costs are substantially lower – average monthly pay is about a quarter of the level in Brussels.
Audi’s restructuring announcement sparked a furious response. Sor Hillal, General-Secretary of the FGTB (Fédération Générale du Travail de Belgique) trade union, blasted what he called “rampant deindustrialisation.” As tensions threatened to spiral out of control, workers at the plant, returning after the summer, were locked out after seizing the keys to nearly 300 new and unfinished cars.
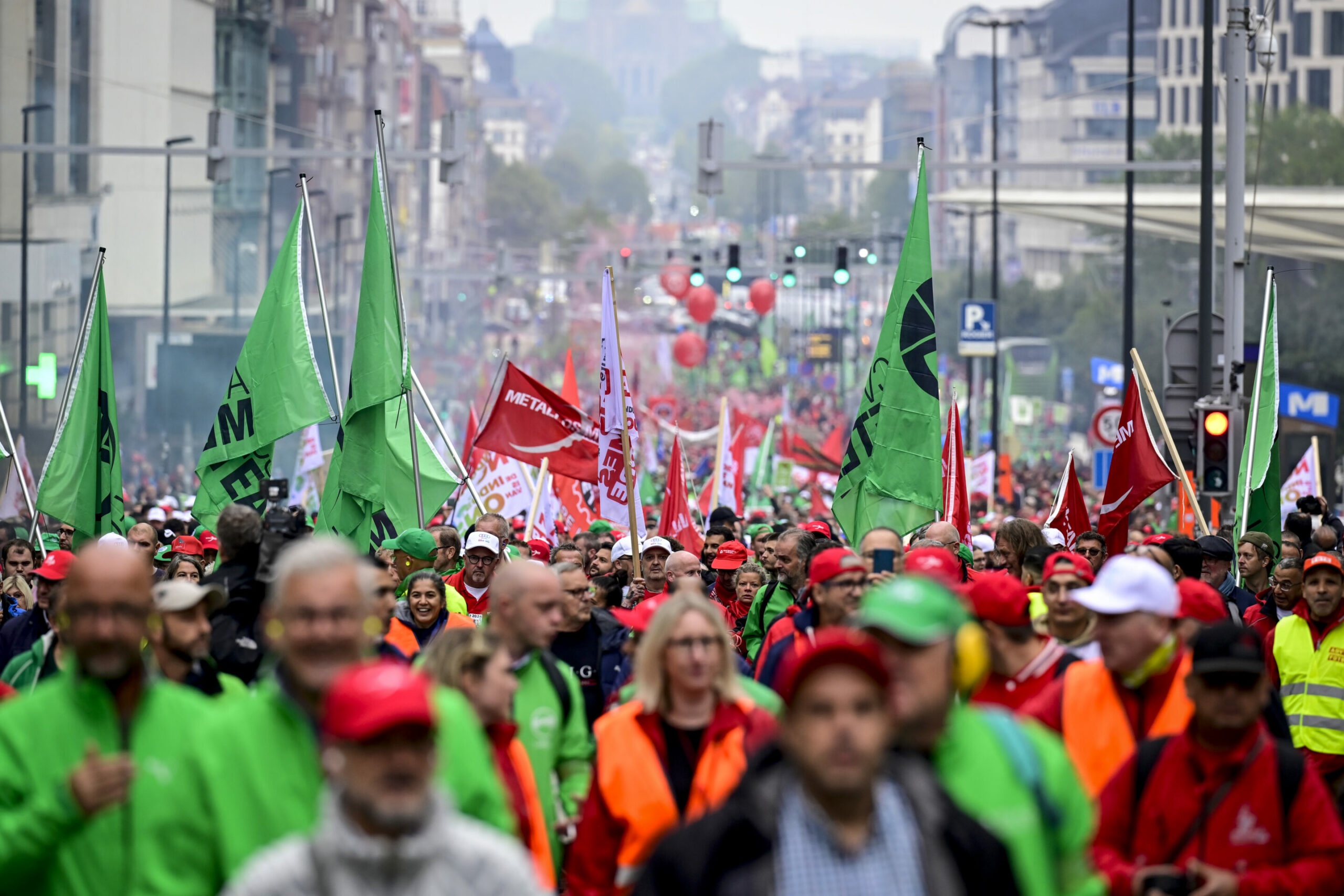
Protestors pictured during a demonstration by Audi Brussels workers supported by the national trade union in solidarity, on Monday 16 September 2024 in Brussels. Credit: Belga / Dirk Waem
While Audi management and unions agreed to resume production, thousands of demonstrators took to the streets of Brussels to express solidarity with the Forest workforce.
New investors or buyers have been sought, with longtime Volkswagen Group importer D’Ieteren and Chinese carmaker NIO mentioned as possible white knights.
D’Ieteren was thought to be considering turning the site into a reconditioning centre for used cars, also known as recon, which is the process of repairing and restoring all aspects of the vehicle before resale. And while NIO was linked to the plant, CEO William Li dismissed the notion. “How could NIO afford a factory that Audi cannot afford,” he told a Chinese news site.
Audi says that it has already looked at more than 20 alternative business models but found no economically viable solution for the plant.
In the meantime, it has launched talks with unions under the so-called Renault Act, introduced in 1998 after the sudden closure of the French carmaker’s factory in Vilvoorde with the loss of around 3,500 jobs. The law states that advance notice must be given of mass redundancies and that the government can demand repayment of state subsidies (which could amount to at least €20 million in tax incentives and aid for greening and training at Audi Brussels).
‘Wrong bet’
The Brussels plant was built in 1948 by D'Ieteren, and since then, countless models have been made there, from the American Studebaker to the VW Beetle and Golf to the Seat Toledo and Porsche 356 to electric Audis. The plant changed hands in 1970 when it was sold to Volkswagen, and again in 2006, when Audi took it over. But this time, it looks like the end of the road for carmaking in Brussels.
So where did it all go wrong? I asked four experts for their views on the Belgian carmaking sector and whether Audi could have done anything to avert the present crisis.
First up is Professor Paul De Grauwe, a former senator and one of Belgium’s most distinguished economists, who describes himself as “an avid reader of the Brussels Times”.
He believes Audi made a “strategic mistake” in focusing on high-end electric vehicles. With a range of up to 600km, and prices starting at €91,690, the Q8 e-tron is not cheap. “They made the wrong bet. The problem is they are addicted to the luxury market. The Chinese are much cleverer in developing smaller electric cars and aiming for a mass market.”
De Grauwe, who is an emeritus professor at KU Leuven and lectures at the London School of Economics (LSE), has long predicted a decline in the Belgian auto sector, for three main reasons: globalisation, delocalisation and technological progress. “We shouldn’t be surprised about what’s happened,” he says.
He points to a collapse in domestic car production since the closure of Renault, with Opel shutting its Antwerp base in 2010 with the loss of 2,600 jobs and Ford ending operations in Genk in 2014 with 4,000 redundancies, not to mention thousands more jobs which have vanished in supply chains.
Part of the problem, De Grauwe explains, is that the Belgian industry has concentrated on assembling cars rather than on making them. “We’re a small country and import a lot from our bigger neighbours. The value-added from assembling cars is relatively small.”
Even if the workforce at Audi was to increase its productivity, this would not have helped. “When productivity goes up, it just means prices will fall and so will employment levels.”
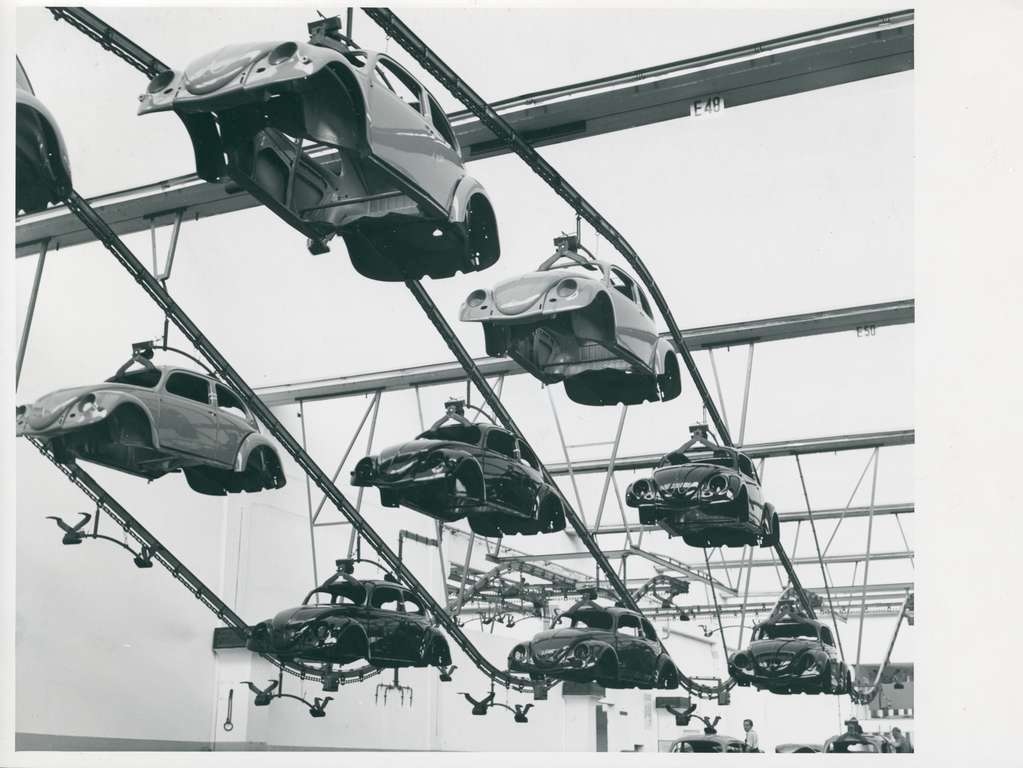
The assembling of the VW Beetle in Forest
He sympathises with Audi, however, over the constraints it has faced due to the site’s location in a congested, built-up inner-city area, where there is no room for further expansion. In contrast, the 78-year-old professor points out that Elon Musk’s Tesla plant at Gruenheide, outside Berlin, has “plenty of space” to grow.
Asked whether the Belgian government should step in and provide additional subsidies to Audi, De Grauwe shakes his head. “No, that’s a very foolish policy. If firms run into trouble they leave anyway. Governments should invest in public goods like education and R&D – not in trying to pick winners.”
Although he paints a rather gloomy picture, De Grauwe insists that there is hope. He is confident Belgians will find “new outlets”, especially, but not only, in the services economy. “I remember people were very pessimistic in the 1970s when the steel and textile industries were struggling, but industry continued,” he says.
Cheaper labour
Leo Van Hoorick, curator of the Autoworld museum in Brussels, shares De Grauwe’s diagnosis of a sector in decline.
“The car manufacturing industry is very sick – not only in Belgium but in the rest of Europe, too. At the end of the 1970s, Belgium was the biggest car producer per capita in the world. But then production began to move to eastern Europe and Turkey where labour costs were cheaper,” he says.
Despite a proud manufacturing history its brands such as Minerva in Antwerp, Excelsior in Zaventem and Impéria in Nessonvaux, Van Hoorick acknowledges that the seeds of the industry’s problems go back a long time.
It was more than a century ago that the government brought in a law which forced foreign carmakers selling more than 250 vehicles in Belgium to build an assembly plant in the country. It seemed a good idea at the time.
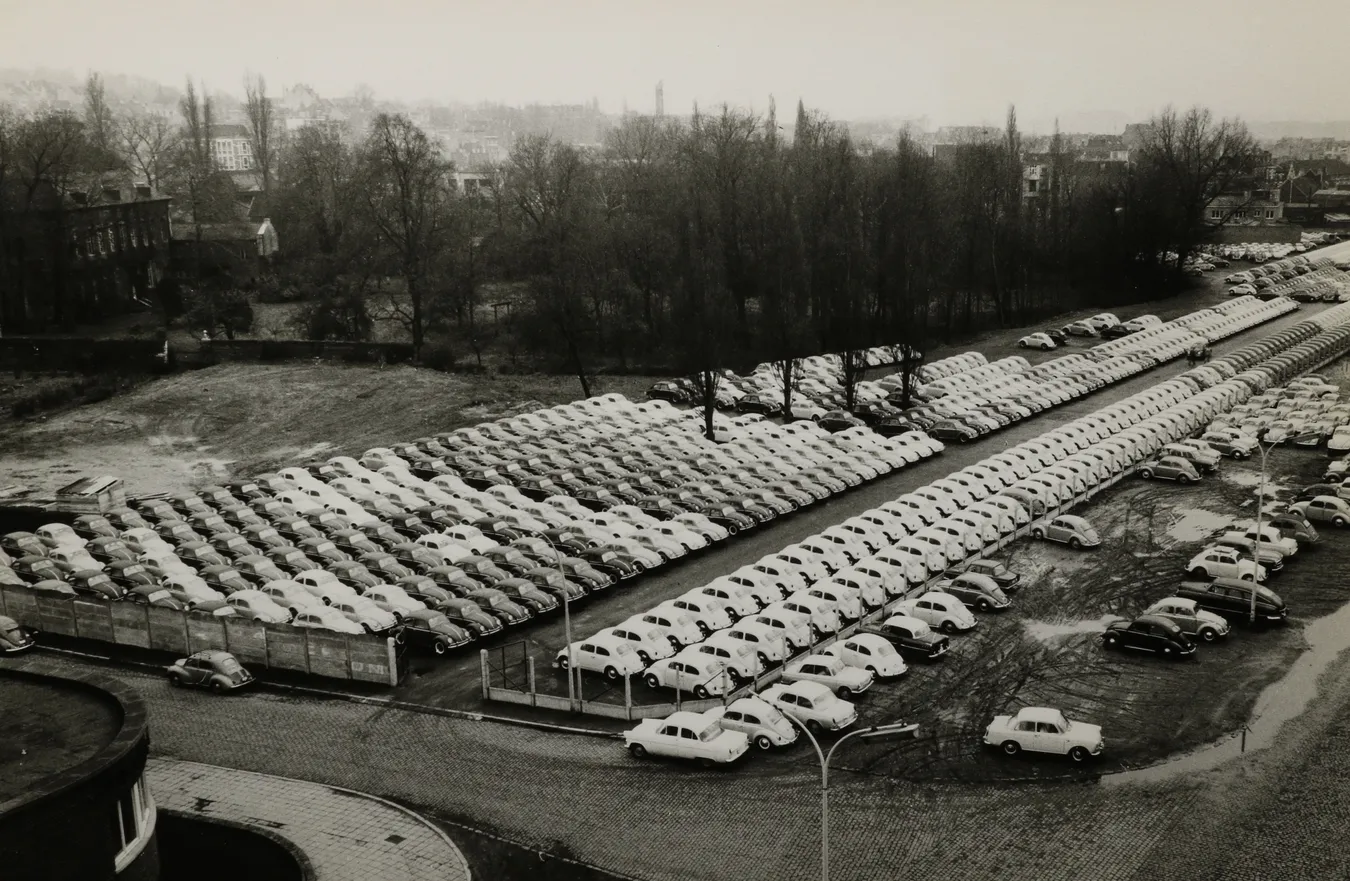
Rows Beetles waiting for delivery
Ford arrived in 1922, followed soon after by GM, Citroën and Renault, with Peugeot joining them just before the Second World War. The plants created thousands of jobs.
“It was easy to import parts through the port at Antwerp – and, thanks to tax breaks, it was much cheaper to assemble cars in Belgium than to import the finished product,” says Van Hoorick.
But this also meant there was less incentive for Belgian firms to design and build their own brands. Excelsior was bought by Impéria which shut in 1948, and Minerva disappeared in 1956.
If poor decisions with unintended consequences were made in the past, Van Hoorick points to two much more recent, inter-connected “major errors”.
“One of the biggest mistakes we’ve seen is the fault of the European Union,” he says, referring to a law which will require all new cars and vans sold in Europe to be zero-emission from 2035. “The infrastructure for electric vehicles wasn’t there and the market didn’t follow. They hoped the market would expand, but it hasn’t yet,” he states.
Audi’s decision to focus entirely on electric cars at its Brussels plant was equally misguided, in his view. “Audi had to build a completely new assembly line. Electric cars are much heavier than their internal combustion engine equivalents. The battery alone typically adds 500-600kg, so the floor in the factory had to be strengthened. In fact, they built a completely new building within the building – and only five or so years ago. It was a very big investment.”
Van Hoorick also highlights what he describes as long-term workforce issues at Forest. “I’m not surprised the factory is closing. There were always problems there, with strikes being called for ridiculous reasons like a shortage of coffee. You never hear of union trouble at Volvo in Gent,” he adds.
Looking at the bigger picture, he predicts that Audi’s factories in Germany will also come under increasing competitive pressure. “Manufacturers prefer to close factories abroad first so they will keep plants in their home market open for as long as possible. Remember, the same happened with Renault at Vilvoorde. It was said to be the firm’s most efficient factory in Europe, but headquarters shut it rather than close plants in France,” he says.
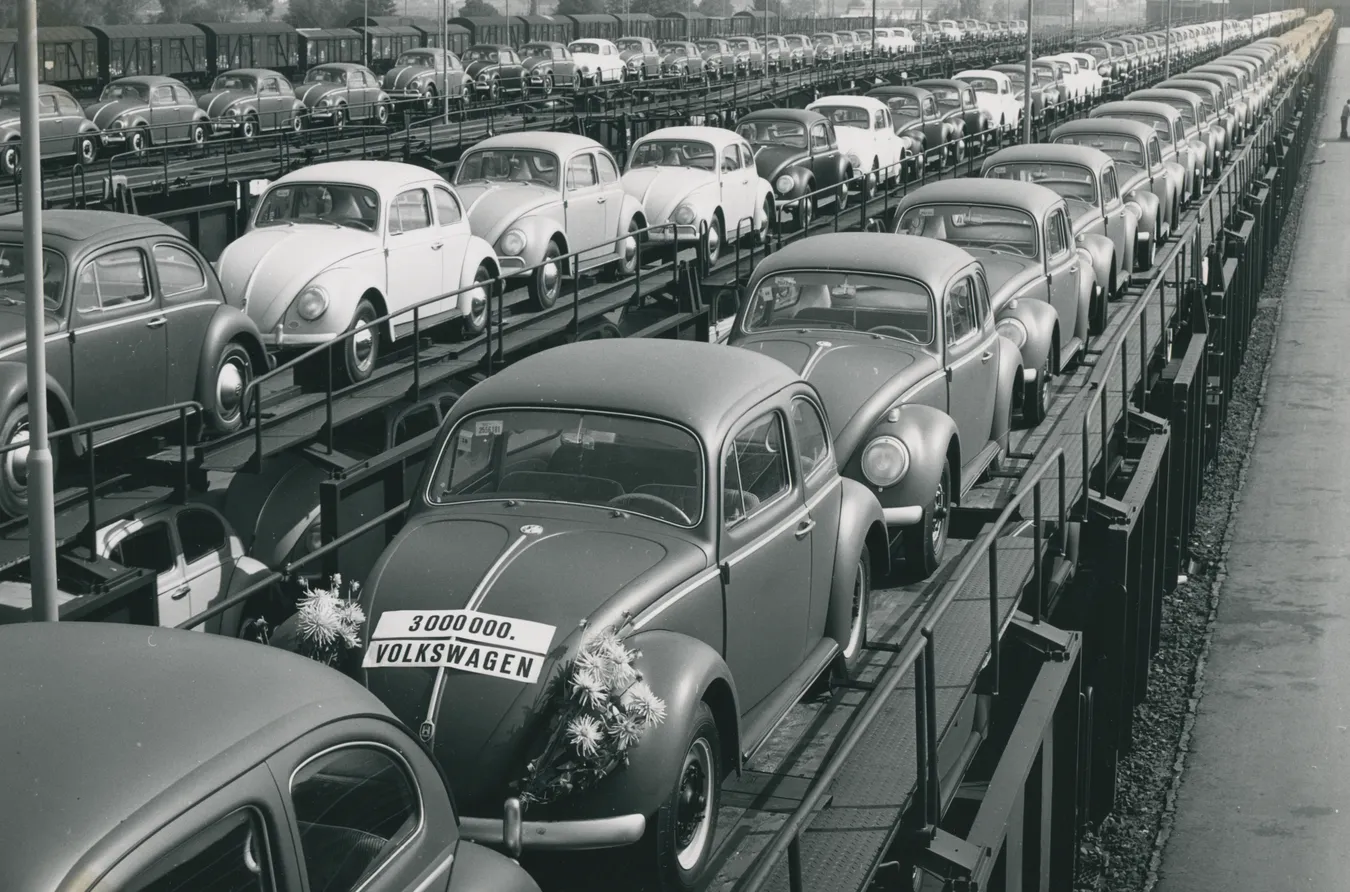
Brussels-made Beetles on train transporters
Steering the transition
Jude Kirton-Darling, general secretary industriAll Europe, a trade union federation, takes a different view. She insists a solution must be found to save the plant and avoid what she terms “destructive restructuring”.
While acknowledging that Audi was “slightly ahead of their time” and “bet on the wrong horse” when making the decision to transform its Forest site for EV production, she says it would be “wasteful to allow the plant to close and see everything stripped away.”
“If production capacity is lost, it’s a significant loss for Belgium more generally,” she warns, while taking issue with “liberal economists” who question the validity of subsidies.
“In my experience, if you’re trying to steer a transition to emission-free vehicles, you need an industrial policy that allows the stimulation of that transition. It’s naïve to think you can stimulate such a transformation and the massive cultural shift required without doing this,” she says.
To prove her point, she refers to the US Inflation Reduction Act (IRA) and its tax incentives to boost electric vehicle production. The 2022 law also benefitted the car sector in Mexico and Canada because they are part of a free-trade bloc with the US. “The IRA actually encouraged Audi to build its smaller A6 in Mexico,” she adds.
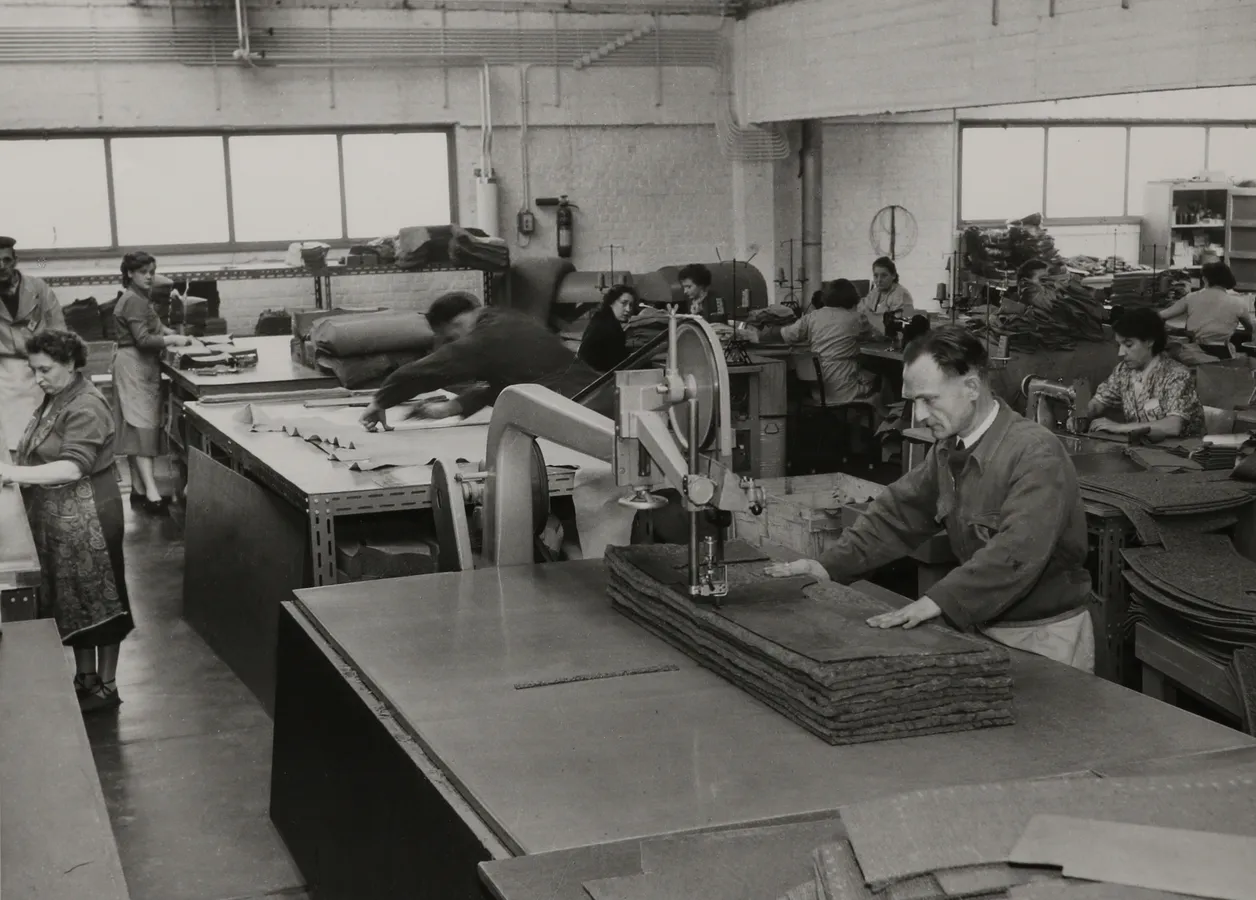
The upholstery shop at the Forest plant
A former member of the European Parliament, Kirton-Darling is scathing about what she sees as the lack of a continent-wide industrial policy. “What we’re seeing is the rhetoric of an industrial policy but with resources stripped away - and a return to austerity.”
She also criticises the EU law requiring all new cars to be zero-emission in just over a decade. “We’ve never taken a policy on a specific date, but a target without a plan will always fail. Without a plan, you don’t get to your destination. It’s like going on a journey without a map.”
Less manufacturing
The fourth expert is Brieuc Janssens, Brussels manager for Agoria, the Belgian federation of technology companies. Like the others, he is “unsurprised” by the developments at Audi.
“The context is tough – we see less and less manufacturing in Brussels. But we need to create jobs here which aren’t just in services or administration,” he says.
Janssens, who took part in recent hearings on the current crisis at the national Parliament (Audi’s management was also invited but failed to attend), fears that it could be very difficult to find an investor who will come up with a satisfactory offer.
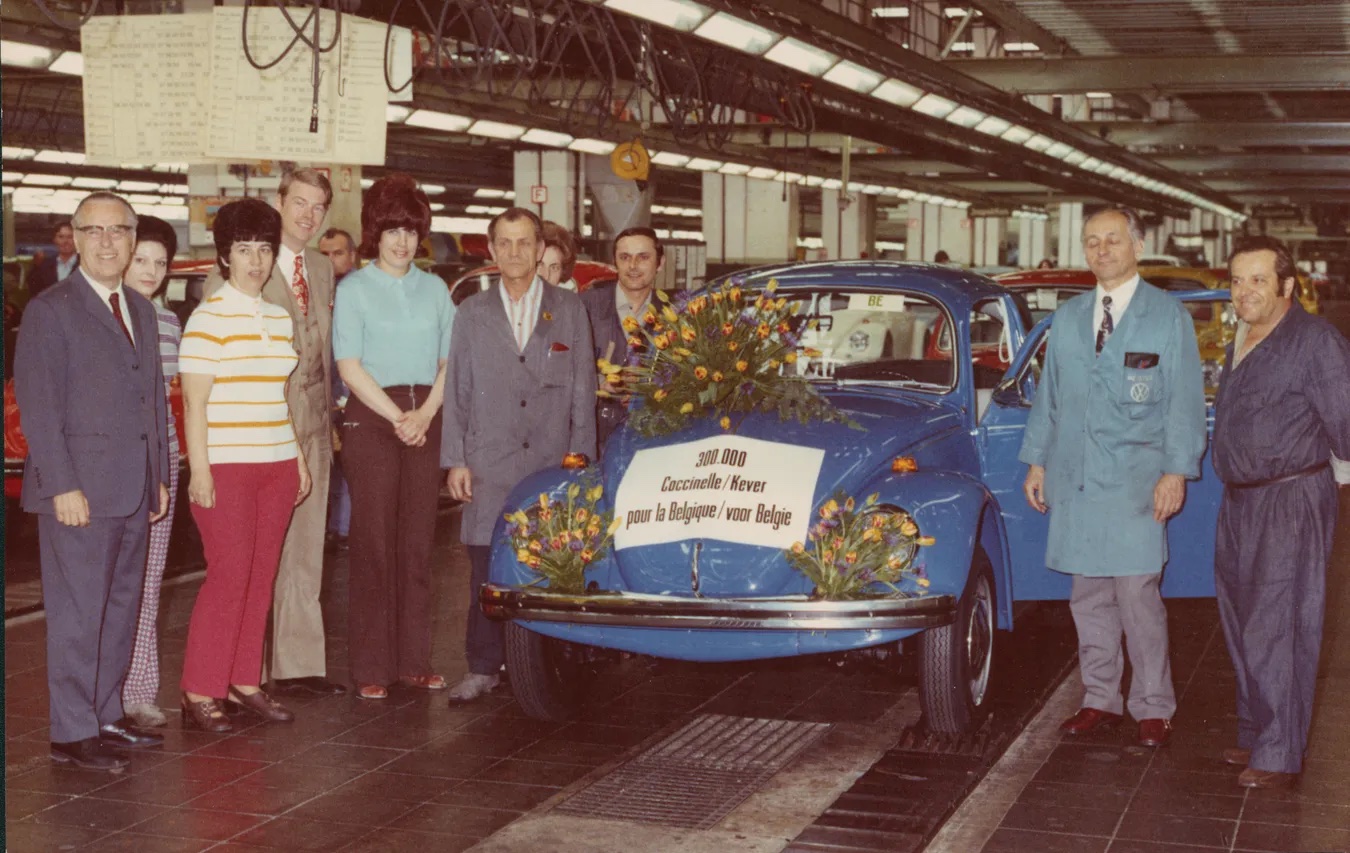
The 300,000th Beetle made at the Forest plant
“It might be that the region will end up buying the plant,” he suggests. “This happened with the Ford site in Genk and Caterpillar at Charleroi which were sold for a euro. What we don’t want is to see the land sold off for housing. We need to keep manufacturing jobs in Brussels.”
In the case of Genk, the site was transformed into various units including logistics operations. It was “very dynamic, involved a lot of upskilling and saved jobs,” says Janssens. The initial regional ‘takeover’ at Charleroi was less successful with many jobs lost and the authorities have since decided to follow Genk’s example by splitting up the site and targeting the logistics sector.
For Janssens, the ideal long-term solution for Forest is a public-private partnership, based on a strategic plan that focuses on three priorities: industry (“retaining manufacturing jobs”), R&D (“creating more sustainable jobs”), and close links with high schools and universities (“to give opportunities to the young”).
Political intervention
In October, outgoing Prime Minister Alexander De Croo met management and union representatives, and called for a social plan to protects Audi Brussels employees and suppliers.
Former Belgian Prime Minister Elio Di Rupo, now an MEP, made his views clear about the stark situation facing Audi Brussels in a question to the European Commission, co-signed by fellow socialist MEPs Estelle Ceulemans, former general secretary of the FGTB Brussels trade union Kathleen Van Brempt and Bruno Tobback.
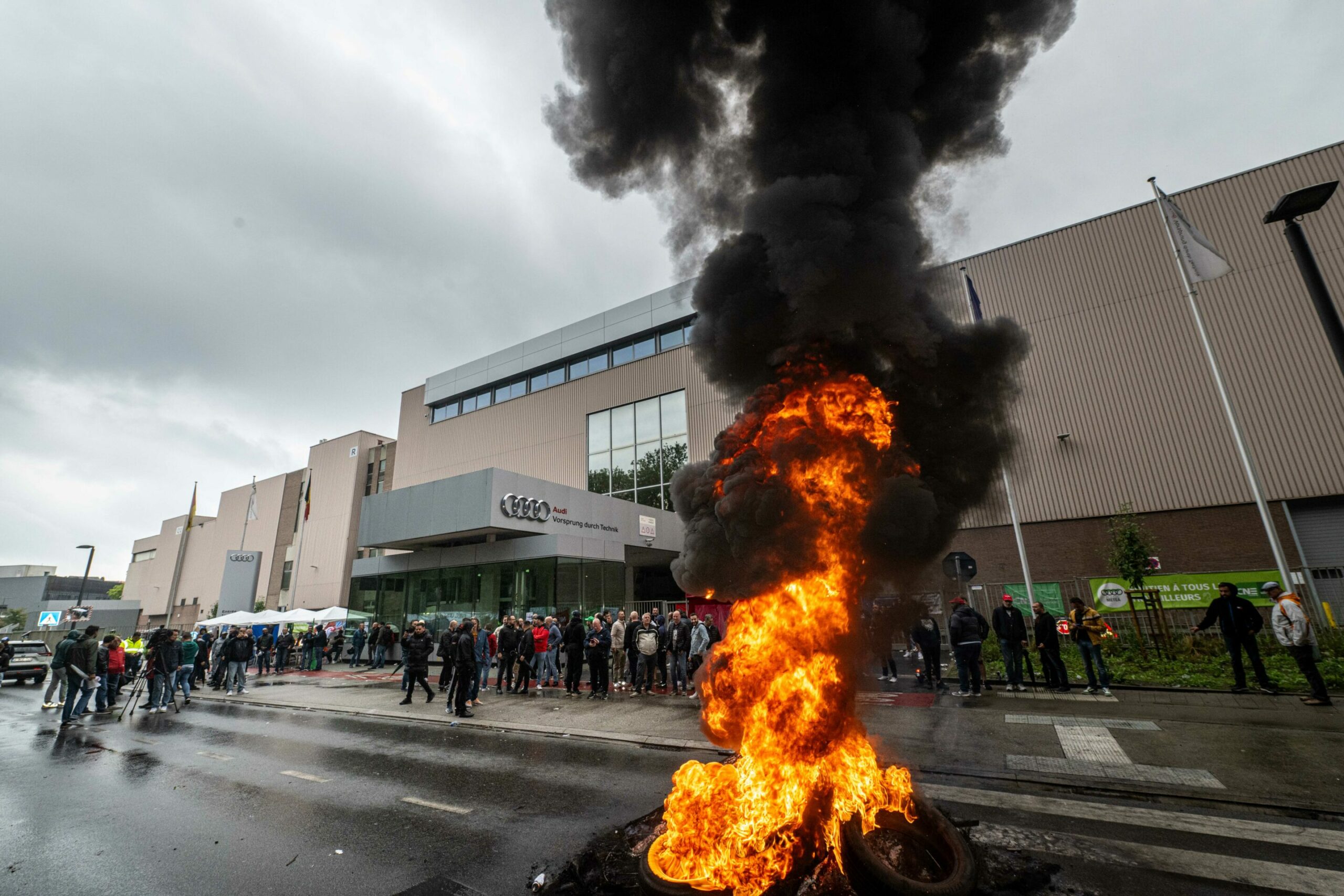
Workers are gathered outside of the Audi Brussels plant, in Forest, Brussels, Monday 09 September 2024. Credit: Belga / Jonas Roosens
It calls for “the preservation of jobs and production, and safeguarding and further developing of green innovative technologies and industry within Europe”, adding that the “reindustrialisation of Europe needs to go hand in hand with measures that encourage local manufacturing”.
The MEPs asked the Commission to spell out how it plans to prevent the closure or relocation of manufacturing sites crucial for sustainable transition and what incentives it will create. At the time of writing, the Commission was yet to reply.
It’s not the end
Meanwhile, back at the plant, spokesperson Peter D’hoore confirms that around 85% of Audi Brussels’ 3,000 employees have now returned to work. Of those, around 2,000 are directly involved in production. “We have two shifts working eight hours. Our current target is for each shift to produce 12 cars per hour,” he says.
Asked what the mood is like among the workforce, D’hoore is surprisingly buoyant. “I have a positive outlook,” he insists. “We’re not at the end.”
Related News
- Audi Brussels ends search for buyer as last potential candidate withdraws
- Europe's dying industry: Thousands attend Brussels Audi march
- Closing time for Audi Brussels? Unions fear for thousands of jobs
A brief history of Audi
Audi was founded in 1909 by German engineer and automobile pioneer August Horch, five years after creating a business he named after himself. In the early 1930s, Audi and Horch merges with DKW and Wanderer to form Auto Union, which uses four interlinked rings as its logo.
Richard Bruhn, a committed Nazi party member, is chairman of Auto Union from 1932-1945. Released from captivity after the war, he relaunches the business with support from the US Marshall Plan. (In 2014 Audi commissioned a study into Auto Union’s wartime record. It found the company worked with the SS to build seven camps where at least 3,700 prisoners were put to work. It also employed 16,500 forced labourers at its factories in Zwickau and Chemnitz).
In 1958, Daimler-Benz takes an 87% holding in Auto Union, increasing its stake to 100% a year later.
In 1964, Volkswagen acquires 50% of the business and relaunches the Audi brand.
In 1969, Auto Union merges with NSU Motorenwerke, creating Audi NSU Auto Union, which ultimately becomes Audi.
In 1970, Hans Bauer, a member of Audi’s advertising department, comes up with the slogan ‘Vorsprung durch Technik’ (Progress through Technology).
In 2015, Audi admits that at least two million of its cars are involved in the Volkswagen diesel emissions testing scandal.
Today Audi produces cars in many worldwide locations. In addition to Brussels, there are three Audi plants in Germany at Ingolstadt, Neckarsulm and Zwickau, and others in Mexico, Slovakia, Spain, Hungary, Spain, Russia, Brazil, India, and China (six locations).
Timeline of the Forest plant
1948: Pierre D’Ieteren lays the first brick for a new car plant on the outskirts of Brussels. He signs a contract with Volkswagen to become its official Belgian supplier.
1949: The first car rolls off the assembly line, a Studebaker.
1954: The plant starts producing the Volkswagen Beetle.
1961: Among a roster of brands, the factory also assembles the Porsche 356.
1970: Volkswagen takes over the Forest plant. It produces its millionth VW Beetle.
1975: Pierre D’Ieteren and his wife die in a car crash – in his Audi.
1980: The plant starts producing the VW Golf.
2001: Production of VW Lupo begins.
2004: Production of the Audi A3 starts.
2005: Foundations laid for a state-of-the-art automotive park for supply and logistics. A bridge connects it to the production halls.
2006: Volkswagen moves VW Golf production at Wolfsburg and Mosel. Following a restructuring agreement, partly brokered by then-Prime Minister Guy Verhofstadt, 2,200 jobs are saved in Forest as it is sold to Audi.
2007: Audi takes over the plant. It continues to produce the VW Polo for two years.
2010: Start of production of the Audi A1, the first model to be made exclusively in Brussels.