Bikes whizz by as you wait at a pedestrian crossing. On the other side, you wave at your friends from all over the world. You pull on a cable above your head to play some music before stopping by a lunch stand. Finally, you are off to witness a “marriage” and go for a trim.
Sounds like a charming little village, right? In a way, it is. It’s the Volvo car manufacturing plant in Ghent, home to 6,500 workers made up of 80 nationalities. With a car rolling off the line every 79 seconds, it is run with an efficiency that most village mayors would envy.
Volvo Cars Gent has been running continuously since the first car – the Amazon – rolled off the belt in 1965. It was the second Volvo car manufacturing facility, and the first outside of Sweden.
“A young engineer, Lars Malmros, was sent to scout sites in Europe,” explains Pieter Philips, my tour guide at the colossal plant in the city’s harbour. “They visited Hamburg, Bremen, Berlin. They visited Antwerp and Rotterdam. They did not come to Ghent.”
Buoyed by the fact that an independent importer was doing some light assembly of Volvo cars in Brussels, Ghent’s city councillor responsible for the port invited the engineer for a visit. As the story goes, there was an evening of wining and dining, and the question was asked: “What do you need from us to build this plant here?”
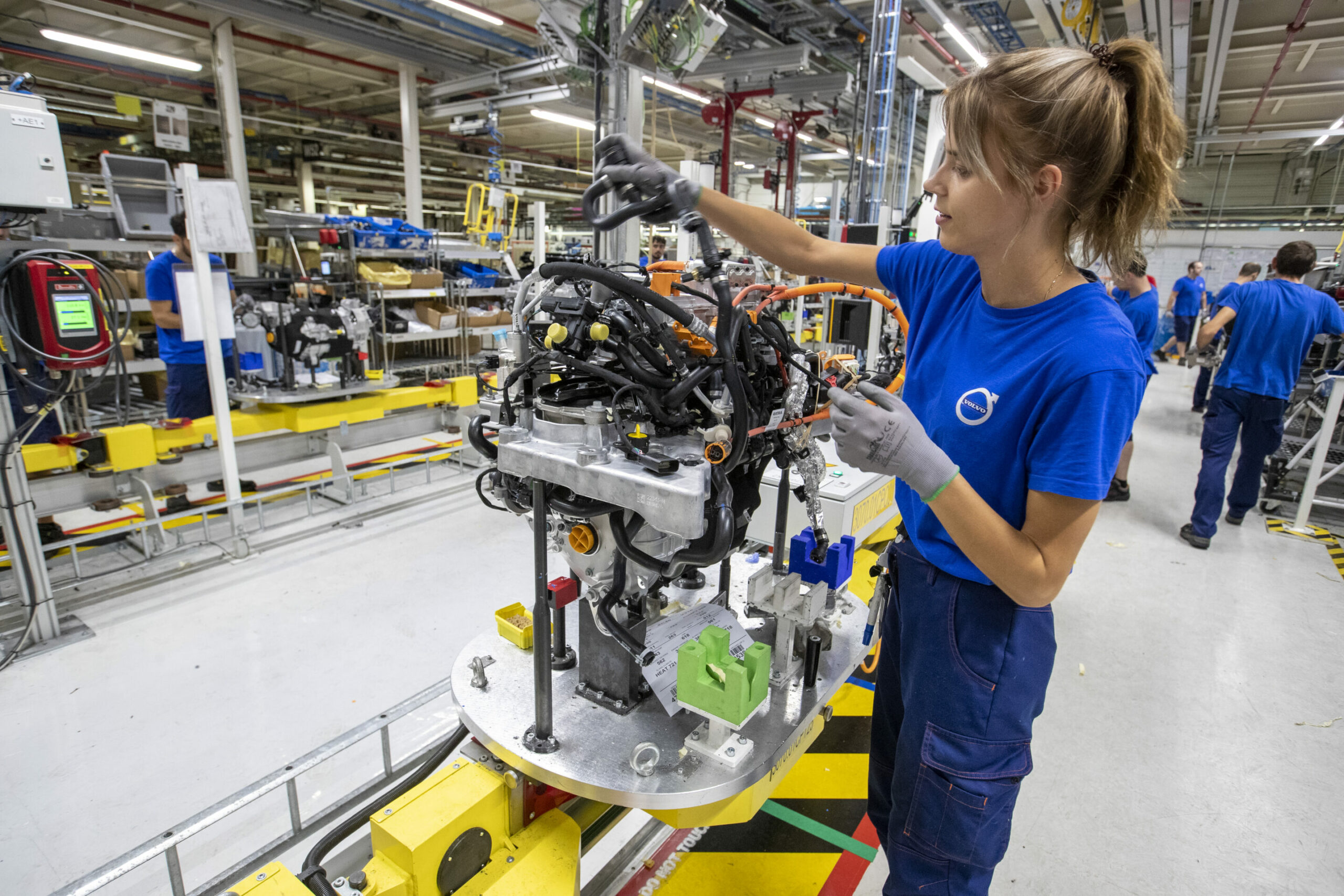
The Volvo Cars plant pictured during a visit to the Volvo Cars plant, during a VOKA summer internship for politicians, in Gent, Monday 12 September 2022. Credit: Belga / Nicolas Maeterlinck
“Lars sketched the design for the plant on the back of a menu,” says Philips. “He said, ‘That’s what I want’. And they said, ‘OK, we’ll arrange it.’”
And they did. While Ghent is 30 km from the sea, its connection via the Ghent-Terneuzen canal and Scheldt river is solid. It had the road and rail connections and the technical schools it needed to make the new plant a success.
The Ghent facility operates 24 hours a day, five days a week in three shifts. Philips himself worked in the steel division at Volvo Cars Gent for more than 35 years until his retirement. Tours of the plant are often given by former workers because no one knows it better than they do.
Cars start out in the welding division, before moving to painting and then final assembly and trimming. In the assembly section, Pieter walks me past the wall of fame – models that have been cut in half from top to bottom and mounted high on the wall. Belts bring undercarriages past workers who grab tools and parts to perform various tasks. If they are missing a part, they pull a cord above their heads, which plays a specific piece of music, alerting the supervisor that help is needed.
Thousands of robotic arms of varying sizes do the heavy lifting and precision work, like placing the windshields. One of the most impressive feats in assembly is the joining of the body of the car to the undercarriage. It’s fully automated and referred to as “the wedding”.
Volvo Cars Gent – part of Volvo Car AB, now owned by China’s Geely Holding – is currently manufacturing the luxury crossover SUV XC40 (hybrid and electric) and the fully electric compact SUV EX40, as well as the crossover electric cousin EC40. The V60 hybrid body is manufactured in Sweden and sent to Ghent for painting and trimming. Ghent will also produce the fully electric subcompact EX30 starting next year. New Volvos are only built once sold to a customer, so workers might see an XC40 one moment, and an EC40 the next.
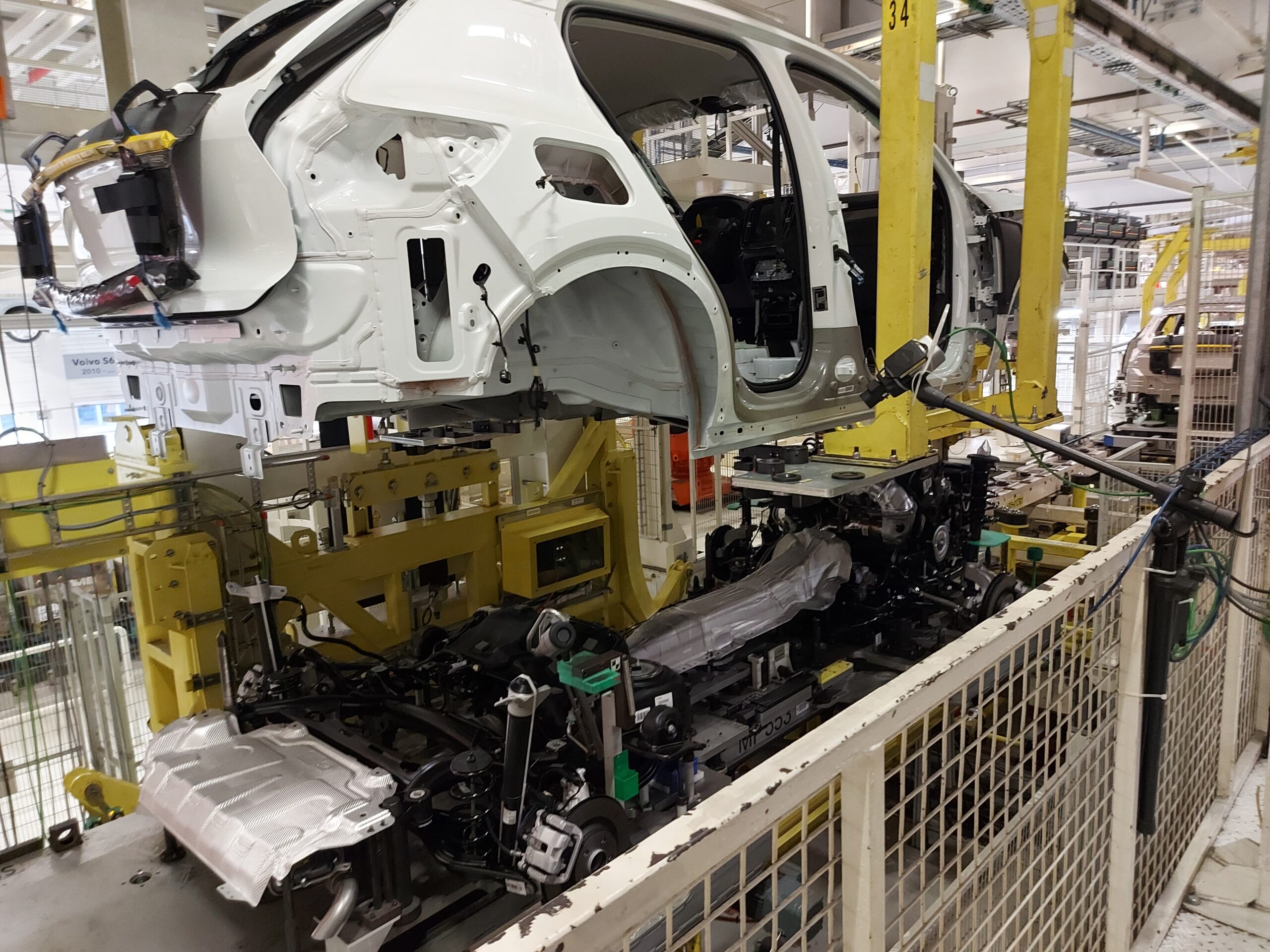
"The wedding": a robot used in the assembly line at Volvo Ghent
Defaming remarks and inappropriate suffering entertainment are omitted, because even the Swedish/Belgian subsidiary the Chinese Geely Holding knows from experience that these kinds of doom scenarios can just fall out of the blue. With an annual production of 230,000 passenger cars and a workforce of 7,000 employees, Volvo Ghent is currently one of the most important (and largest) employers in Belgium, but even that offers no guarantees, as the bankruptcy battlefield from the past teaches us.
The Chinese car conglomerate is already anticipating the high import tariffs for Chinese cars that the European Commission wants to introduce in the short term, ranging between 20 and 50 percent. China is competing in unfair competition by subsidising its own manufacturers and supplying cheap raw materials, said Commission President Ursula von der Leyen, who said she hoped to “be able to somewhat dam the overflow of over-subsidised Chinese electric cars.
In response to that penalty levy, Volvo immediately announced that it would no longer build its new small electric SUV EX30 only in China, but also in Ghent. Volvo Ghent will still be able to benefit from the increased import tariffs in the coming years, but the decision to build the EX30 in Europe is completely independent of the increased import tariffs, according to Volvo CEO Jim Rowan. "We build our cars where we sell them and the Volvo EX30 is a greater success in Europe than in China." In the Belgian market alone, the mini-SUV caused a sales increase of no less than 30 percent.
Volvo Car Ghent was already the largest factory of the brand, but it goes without saying that the Chinese family expansion cannot be realised without heavy investments in capacity expansion and personnel.
How can people recognise a Volvo? Philips points to the taillights. “They’re shaped like Thor’s hammer,” he says.
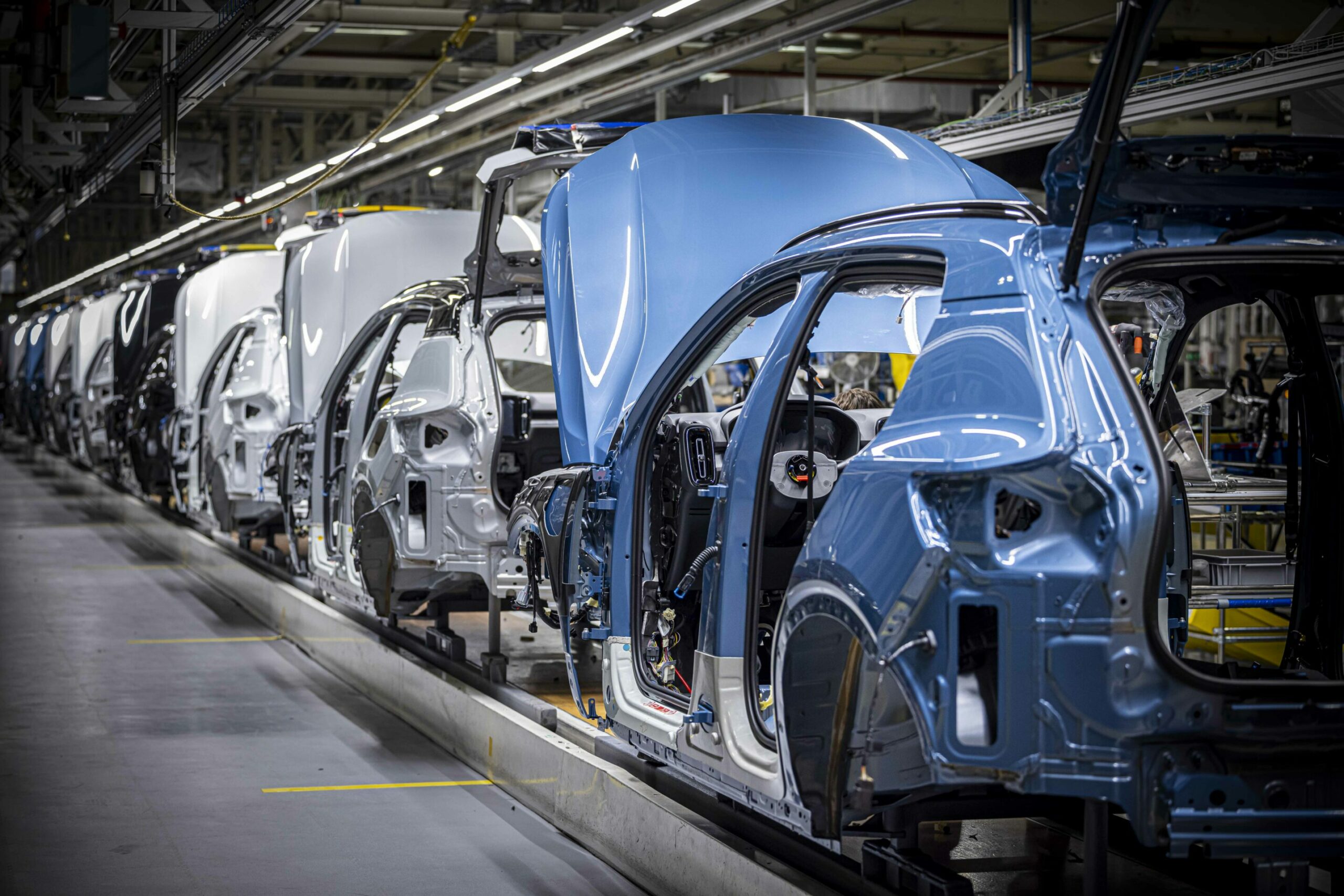
The assembly line today at Volvo Ghent
Volvo thrives
One by one, car manufacturing plants in Belgium have shut their doors: Renault Vilvoorde in 1997, General Motors Antwerp in 2010, Ford Genk in 2014. In 2007, Volkswagen restructured the plant in Brussels to produce its Audi brand. And now Audi is in trouble.
Conversely, Ghent’s Volvo facility pumps out more than 230,500 cars a year – as many (and in some years more) as the headquarters in Gothenburg. Together the plants produce two-thirds of all the brand’s cars, despite there being four more manufacturing plants – one in the US and three in China. In the face of it all, Volvo Cars Gent isn’t just surviving, it’s thriving.
Which begs the question: Why? “Because of that,” says Geert Bruyneel, laughing and pointing to a large-scale photograph of a Volvo vehicle. I get his point. It’s the car, stupid.

The Volvo Cars plant pictured during a visit to the Volvo Cars plant, during a VOKA summer internship for politicians, in Gent, Monday 12 September 2022. Credit: Belga / Nicolas Maeterlinck
We’re sitting in a conference room at the plant, which Bruyneel ran from 2010 to 2013. A Belgian, he joined Volvo in the 1980s as an engineer and has since worked from Sweden, Ghent and China, managing quality control and global supply chains. These days he’s back in Sweden acting as a senior advisor to the brand’s Scottish CEO.
But today Bruyneel is in Ghent to talk to me about what makes Volvo Cars tick.
“I have always said that there are two things that are important,” he says. “We continue to invest in this plant to make sure it’s up to date and capable of launching new cars. You have to continue to be relevant to the company. This plant has always been a hub of highly competent people, both on the production lines and in engineering.”
He points to employee recruitment and development, which he sees as a crucial aspect of Ghent’s success. “More and more we are a tech company, so we have to recruit people with the right background - and of course we continue their development here. We stimulate this enormously, working to empower people to grow in their jobs, to take accountability and ownership.”
The second thing, he says, is location, location, location. “Belgium is an excellent hub for both trade and the supply chain. The majority of our customers are in Western Europe. And because we are close to the sea, we export to the US. We’ve benefitted from that since the beginning. With the disruptions that go on in the world, it’s important to have a low-risk supply chain.”
Zero emission ambition
All of Volvo’s new cars are either hybrids or fully electric, with the goal of producing only fully electric models by 2030. On the very day of my visit to the plant, receives – with much ceremony – the customer who bought the one-millionth XC40/EX40. It is the first time any Volvo plant has produced one million units of the same model.
Still, Volvo’s electric models are being outsold by Tesla and Volkswagen in the European car market. “We are producing premium cars,” says Bruyneel. “We’re not competing for the last euro. We are not trying to get the highest market share or the highest volume. We want to stick to the roots of our brand.”
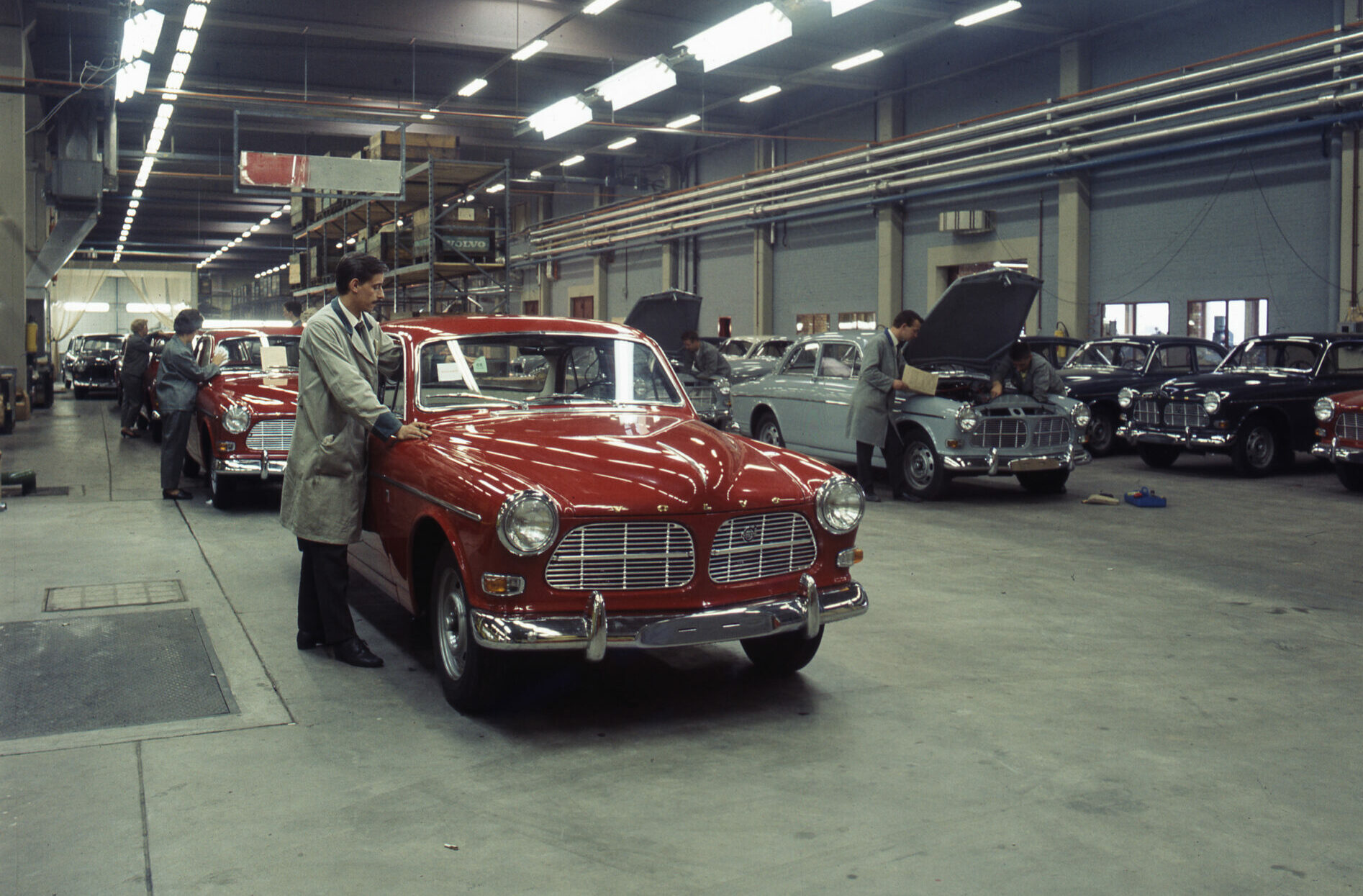
The Volvo plant in the 1960s
A key factor in Volvo’s reputation is safety. In 1959, it invented the seat belt, handing out the design freely to other manufacturers. Each car contains 400 different kinds of steel – from crush-proof boron alloys to impact-absorbing crash steel – a high number for the automotive industry.
“We are pioneers in safety,” Bruyneel states, as he points to the future of self-driving vehicles. “You really have to trust a car if you’re not driving it,” he chuckles. “That requires extreme confidence. We’re not there yet.”
The implication is that Volvo will get us there. “If you are not an industry insider, you cannot comprehend how strong that safety culture is. We continue to try to be a pioneer in that, and it is keeping us at the top of the pyramid.”
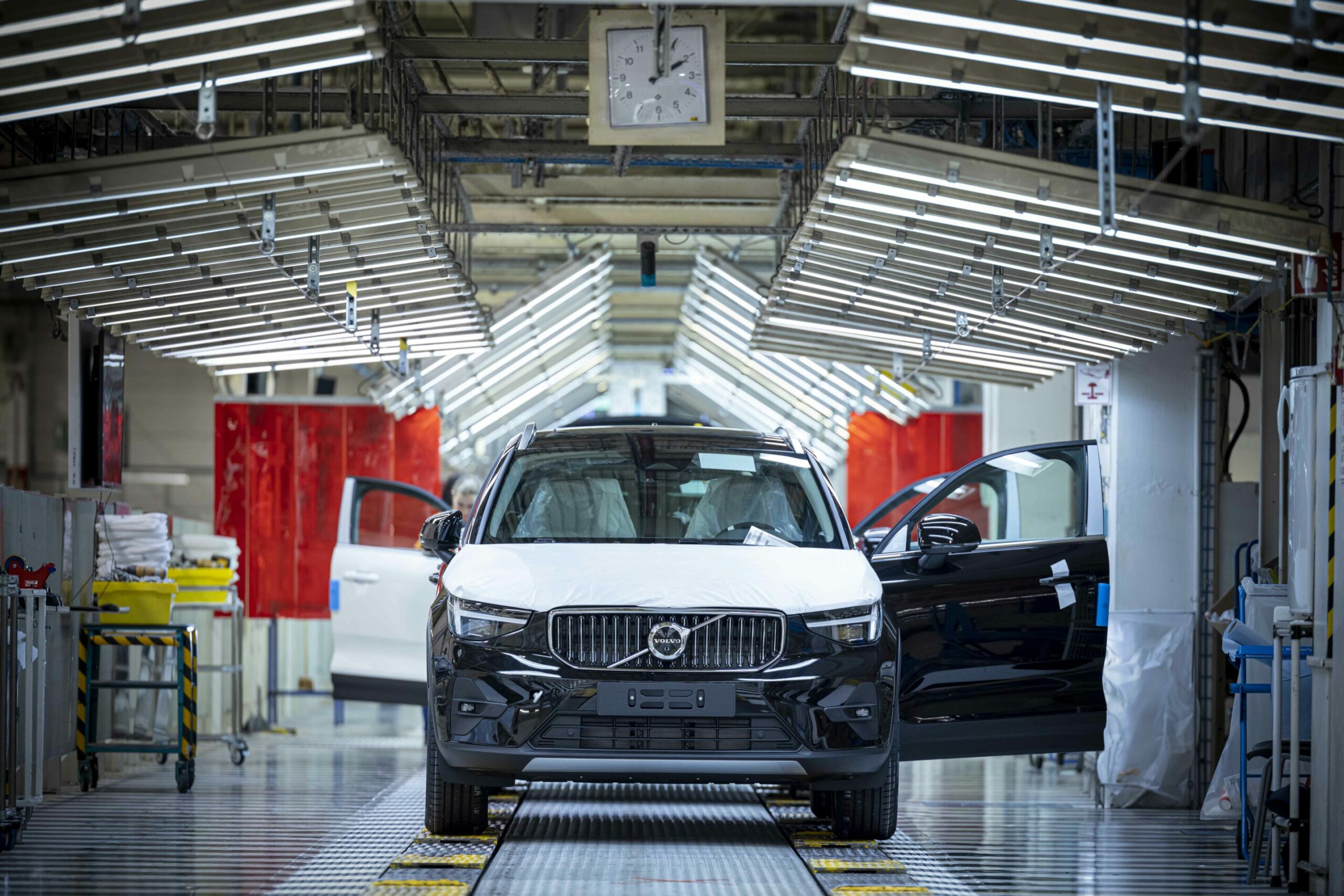
A Volvo car in the assembly line
Considering Belgium’s strong union culture and the size of Volvo Cars Gent, the lack of industrial action is quite remarkable. So infrequent are labour disputes that everyone is still talking about the big three-week strike of 1978. “It was then that the foundation was laid for future labour negotiations,” explains Dirck Bogaert, one of Volvo’s ACV union representatives. “The CEO at the time made the firm decision to position unions as partners rather than the enemy. The idea was: No more strikes.”
Since then, conflicts have led to temporary work stoppages at most. According to Bogaert, this is because a typical top-down approach has been abandoned. Union members are in close contact with the board of directors, and decisions are made with their approval before they are implemented.
Even when Volvo sold the car division to Ford in 1999, and when Ford sold it to the Geely group a decade later, work continued as usual. “We were of course worried when the company was sold to the Chinese,” says Bogaert. “But it quickly became clear that they respected the way we operate. Nothing changed. Quite the opposite: Geely said to stay Volvo, to stay who we are.”
Bruyneel refers to this identity as well in explaining Volvo’s appeal. “There’s this Scandinavian heritage in design and materials but also this special thing, this mystery. It’s a kind of feeling in the brand. It’s more than just metal. You can’t copy that.”
It sounds a bit over the top. But the other evening, my partner and I were sitting at a traffic light. That’s a Volvo in front of us, I mentioned. It was too dark to see the logo, but I saw the taillights – shaped like Thor’s hammer.